Hydrogen embrittlement fracture of bolt
There are many kinds of hydrogen embrittlement fracture, including hydrogen corrosion fracture, white point fracture, hydride embrittlement fracture and hydrogen induced delay fracture. Hydrogen embrittlement fracture of screw usually refers to hydrogen induced delay fracture: hydrogen atom intrudes into the base material of screw, after screw tightening, that is, the screw bears a certain static load (tensile stress) along the axis, after a period of time, brittle fracture suddenly occurs. Hydrogen embrittlement fracture is a common failure mode of screws. The hydrogen embrittlement fracture of screws usually occurs in the joint of screw head and screw or smooth rod and screw thread, which are heat-treated and electroplated high-strength ordinary screw and self tapping screw with high surface hardness. Hydrogen embrittlement of screws usually occurs within 48 hours after assembly. The most direct way to determine whether the screw fracture is hydrogen embrittlement fracture is to observe the fracture morphology. Macroscopic observation with naked eye or low power magnifying glass: the fracture surface of screw hydrogen embrittlement fracture is basically vertical to the direction of maximum normal stress, the fracture surface is flush, without obvious plastic deformation, the fracture surface can be obviously divided into two areas: crack source area and crack growth area, the crack source area is crystalline granular, the color is dark gray, the crack source area starts from the root of the thread, and cracks along the direction of thread rotation; cracks The color of the propagating region is silver gray, and radial stripes can be seen, which converge to the crack source region. Scanning electron microscope or electron microscope microscopic observation: the crack source area is in the shape of intergranular fracture (microcracks exist between the grain boundaries), and there are secondary intergranular cracks. The grain outline is clear, in the shape of crystal sugar. There are a lot of chicken paw marks on the grain surface. The crack growth area is mainly in the form of quasi cleavage fracture (transgranular fracture under normal stress, usually separated along a certain strict crystal surface), At the same time, there are some dimples and intergranular fracture in some areas.
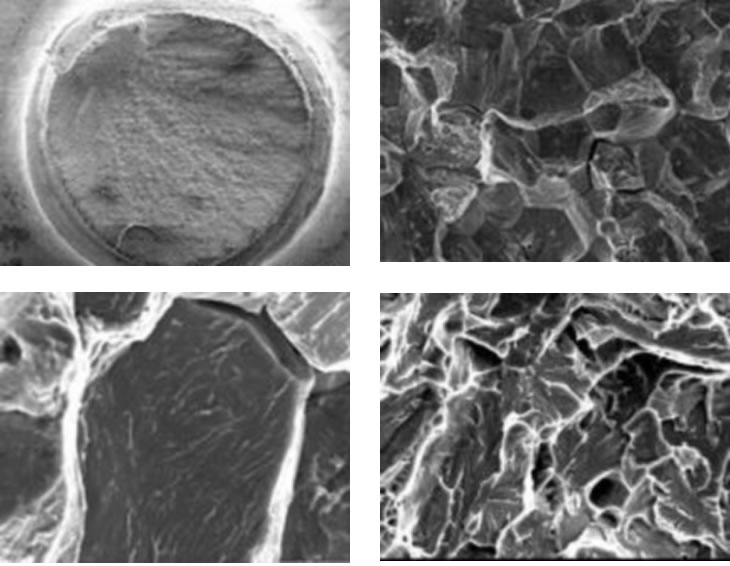
The hydrogen content of screw matrix material is also an important basis for judging whether it is hydrogen embrittlement fracture. The hydrogen content can be measured by oxygen nitrogen hydrogen analyzer, mainly to see whether the hydrogen content is significantly increased compared with qualified screws or screws before plating treatment. There is no strict standard for the allowable hydrogen content of carbon steel materials, but there is no doubt that hydrogen will cause damage to carbon steel materials. The amount of hydrogen content only shows the difference of damage degree to carbon steel materials. The mechanism of hydrogen embrittlement fracture of screws is very complex. Since the problem of hydrogen embrittlement fracture of screws was found in 1940s, the fracture mechanism has been a research hotspot in the academic field, but there is no unified cognition so far. There are four famous theories: hydrogen pressure theory, hydrogen surface adsorption theory, lattice embrittlement theory and dislocation theory. The dislocation theory can explain the characteristics of screw hydrogen embrittlement relatively well. The dislocation theory holds that when the temperature is lower than a certain critical temperature, the hydrogen in the matrix material forms a certain air mass in the process of matrix deformation. When the deformation velocity of the substrate is relatively low and the temperature is not too low, the air mass will move with the dislocation. It has a certain distance from the dislocation, but it is suitable for the movement velocity of the dislocation, so as to screw and anchor the dislocation, so that the dislocation can not move freely, so local work hardening occurs. Under the action of external force, when dislocation moves to the grain boundary or other obstacles, dislocation accumulation and hydrogen accumulation will inevitably occur there. If the external force is large enough, stress concentration will occur at the end of dislocation accumulation, and finally lead to matrix cracking.
The main factors causing the hydrogen embrittlement fracture of screws are the sensitivity of the matrix material to hydrogen embrittlement, the surface condition of screws, the residual internal stress after cold working and heat treatment of screws, the hydrogen invading the matrix material of screws in the manufacturing process, the ambient temperature, the external load after the assembly of screws and so on. The hydrogen embrittlement sensitivity of carbon steel is closely related to its strength. The higher the strength is, the higher the hydrogen embrittlement sensitivity is. The strength is related to the carbon content and microstructure of carbon steel. Experiments and facts show that the hydrogen embrittlement sensitivity of pearlite and ferrite is much lower than that of martensite, and the high carbon martensite with network distribution has the highest hydrogen embrittlement sensitivity. The common screw thread used in electronic products does not need heat treatment, and its strength grade is relatively low. Most of the material microstructure is ferrite or pearlite structure, with low sensitivity to hydrogen embrittlement, and there is generally no problem of hydrogen embrittlement fracture. The high-performance common screw thread or self tapping screw thread must be heat treated, and most of the material microstructure is martensite or high carbon martensite structure The risk of hydrogen embrittlement fracture should be considered. There is a good relationship between the strength and hardness of carbon steel. It is more intuitive and convenient to use hardness to show the hydrogen embrittlement sensitivity of carbon steel. Generally speaking, when the hardness is about 38 HRC, there is a danger of hydrogen embrittlement fracture. When the hardness is higher than 43 HRC, dehydrogenation treatment should be considered. When the hardness is higher than 60 HRC, dehydrogenation treatment must be carried out immediately after surface treatment.
The production practice shows that the pickling process and electroplating process before electroplating are the key links of hydrogen invading into the base material in the manufacturing process, and they are inevitable. The reliable solution is to increase the dehydrogenation process after electroplating. Generally speaking, screws have residual internal stress after cold working and heat treatment. When hydrogen intrudes into the screw matrix material, after a period of time, under the effect of residual internal stress, the screw matrix material may form grain boundary microcracks. Once microcracks are formed, they will not heal. Therefore, the dehydrogenation treatment must be carried out before the formation of grain boundary microcracks. The best dehydrogenation treatment is recommended by GB and ISO standards Within 1 hour after plating treatment of screws.
Dehydrogenation is actually a baking process. The screws are baked at a temperature of 190-230 ℃ and within a specified time. The hydrogen in the screw matrix material is evaporated and irreversibly collected to release hydrogen atoms. Although dehydrogenation can only remove a small part of the hydrogen, it can redistribute the hydrogen in the matrix material and make it difficult to gather to the stress concentration of the screw. Baking time depends on screw specification, hardness of material, coating type and coating thickness. Baking time is usually selected within 2-24 hours, and many standards have recommended baking time. For example, ASTM B 850 stipulates that the minimum baking time of self tapping screw is 2 hours, and the minimum baking time of self tapping locking screw is 4 hours.
It is worth noting that the complete screw plating process also includes passivation treatment, while the passivation film can only withstand a temperature of 60-70 ℃. Therefore, the dehydrogenation treatment must be completed after plating and before passivation, otherwise, the dehydrogenation treatment will damage the passivation film. Hydrogen embrittlement test shall be carried out for the screws after dehydrogenation to check whether the dehydrogenation is complete. National standards of various countries have clearly defined hydrogen embrittlement test methods. The self tapping screw usually uses 80% of the breaking torque as the tightening torque to screw the screw into the standard smooth hole on the test steel plate for 24 hours. After loosening and retreating the screw, screw in again with the original tightening torque. After 24 hours, loosen and retreat the screw, and visually check whether the screw is broken. The ordinary screw or self tapping locking screw is screwed into the standard threaded hole on the test steel plate with its tightening torque. When testing common screw thread, if 4-6 degree wedge plate is used, the test result is more reliable. There is also a very simple and practical method to test the effect of dehydrogenation: take a proper amount of liquid paraffin (completely submerge the screw to be tested) in the beaker, heat and control the temperature at 100-190 ℃, keep the temperature in this temperature range for 5 minutes to remove the moisture in the paraffin, remove the oil trace and moisture of the screw, and put it into the paraffin. If there is bubble in the screw within 10 seconds, it indicates that the screw still has If there is a certain amount of hydrogen and there is no bubble, the effect of dehydrogenation is good.
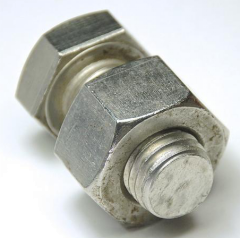
Occurrence and prevention of hydrogen embrittlement of high strength bolt.pdf